Key Insights
AI agents are revolutionizing manufacturing by transforming machine calibration and optimization processes. Leveraging agentic workflows enhances efficiency, minimizes downtime, and optimizes resource utilization, leading to significant cost savings for manufacturers. With proactive maintenance and intelligent monitoring, AI agents prevent machine breakdowns while ensuring superior quality control.
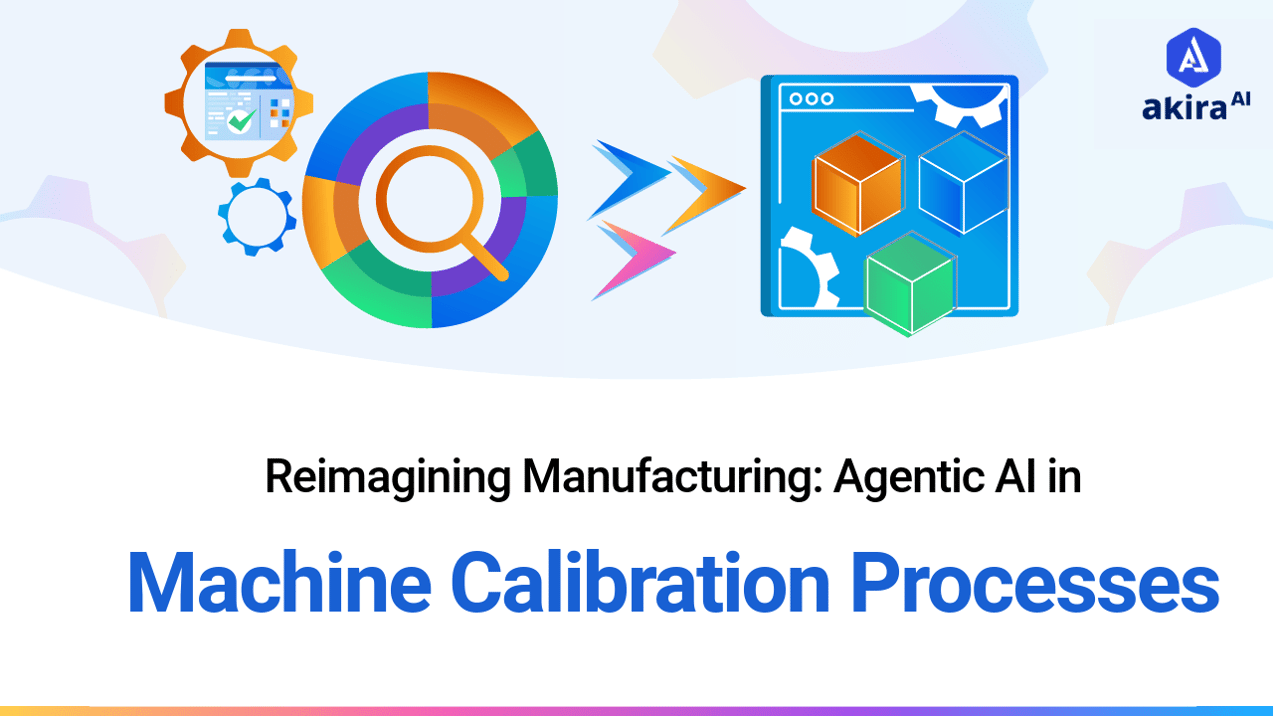
Agentic workflows are transforming manufacturing by enhancing machine calibration and optimization, leading to improved performance and precision. Rather than a revolution, this shift represents adaptability in manufacturing processes. By integrating AI Agents, companies can achieve higher efficiency and better quality control. This blog post explores agentic manufacturing, emphasizing the significance of machine calibration and optimization.
It will highlight various use cases and the advantages of incorporating Agentic workflows into production workflows, showcasing how this technology is reshaping the industry's landscape for the better.
What is Machine Calibration?
Calibration of machines is adjusting or aligning machine parts for proper operation within the limits and for the maximization of the quality of products made. Manufacturing is one of the fields where attention to detail in calibration is paramount because the slightest error will lead to a major shift in the finished good quality, more waste production, and ultimately more costs. Historically, such calibration work has been performed purely manually and has been a lengthy process due to the labor-intensive efforts of specialists who evaluate and make corrections to the equipment. But after that, AI agents came into the picture, and this process was greatly simplified.
A Brief Overview of Machine Calibration in Manufacturing
Machine calibration is essential in manufacturing for maintaining optimal performance and product quality. Leveraging Agentic AI, manufacturers can analyze vast datasets generated by machines in real-time, enabling precise monitoring and adjustments. This objective approach minimizes human error, accelerating the calibration process while ensuring consistency. The implementation of agentic workflows further streamlines operations, enhancing efficiency and allowing for rapid calibration without compromising production standards.
Additionally, agentic AI enhances proactive maintenance by predicting when machines are likely to deviate from their set calibration. By analyzing historical performance data, these intelligent systems can trigger maintenance alerts before issues occur, reducing downtime. This predictive capability ensures that machines operate within optimal parameters, ultimately boosting overall productivity. In summary, integrating agentic AI and agentic workflows revolutionizes machine calibration, helping manufacturers achieve greater efficiency and quality in a competitive landscape.
Traditional vs. Agentic AI Machine Calibration
Feature |
Manual Calibration |
Automated Calibration Systems |
Process |
Hands-on adjustments by technicians, often involve physical checks and subjective evaluations. |
Continuous real-time adjustments using sensors and algorithms that automatically calibrate machines based on performance data. |
Time Efficiency |
Time-consuming; calibration processes can take hours or even days, leading to significant machine downtime. |
Quick adjustments enable rapid recalibration, often in real-time, minimizing production interruptions and maintaining workflow continuity. |
Consistency |
Results can vary due to differences in technician skill and experience, potentially leading to inconsistent product quality. |
High consistency is achieved through standardized algorithms, ensuring that calibration is uniform and reliable across all machines. |
Response to Issues |
Reactive approach; issues are only addressed after they arise, which can result in delays and increased production costs. |
Proactive; predictive maintenance capabilities analyze historical data to anticipate and resolve potential issues before they disrupt operations. |
Data Utilization |
Limited analysis of operational data; technicians may rely on basic measurements without in-depth data insights. |
Comprehensive big data analytics are employed to monitor performance trends, identify anomalies, and optimize calibration processes based on real-time data. |
Akira AI Multi-Agent in Action
The elaborated framework for improving machine performance is a holistic viewpoint regarding the contemporary production system. Advanced data acquisition, agentic workflow analysis, optimization, and full performance control are incorporated into this system in order to maximize work efficiency and reduce time and losses.
-
Data collection Agent: This agent is tasked with collecting data in real-time, especially from IoT-based Temperature, pressure, and vibration sensors. It enhances the operation of equipment by making sure that there is proper and uninterrupted data acquisition.
-
Data Processing Agent: After data gathering, this agent utilizes modern AI technology to manipulate the collected data. This agent prepares the data which has been collected for further processing and business intelligence.
-
Optimization Agent: This agent aims at fine-tuning the performance parameters of the machine. It determines the best configurations that are able to maximize the performance of the machine and minimize any wastage.
-
Adjustment Agent: The adjustment agent downloads the configuration, either automatically or manually. When in autonomous mode the adjustment agent, however, limits itself to extreme altering while ensuring real-time safety thresholds are not exceeded.
-
Monitoring Agent: The Monitoring Agent assesses the performance of the machine after the introduced changes have been made in order to appreciate their effectiveness. It examines output quality, production speed, and energy consumption activity as a basis for enhancing performance.
Use Cases and Applications of AI in Calibration and Optimization
Although a majority of industries have not embraced AI as a solution for machine calibration and optimization, it has started delivering significant benefits in this regard. Below are several such cases.
-
Aerospace and Defense: Given that the aerospace industry is a domain where accuracy matters a great deal, it is of no surprise that other than people, artificial intelligence is used in the calibration of engines and other parts of the airplane.
-
Car Assembly: The automotive domain utilizes machine learning for calibration as well as for optimization purposes.
-
Electronics Assembly: Electronics industries face the challenges of manufacturing smaller, more complex designs, therefore agentic workflow enhancement achieves the required machine calibration with a high degree of accuracy.
-
Medicine: In the area of medicine, errors are intolerable. This is because agentic workflows can perform the calibration of drug production equipment.
-
Energy Sector: Within the scope of green energy, artificial agents are utilized to fine-tune the angle of installation of solar panels and wind turbines with a view of maximizing their performance and minimizing the level of maintenance as much as possible.
-
Manufacturing: AI agents also enhance the efficiency of certain processes in general manufacturing. For instance, the accuracy of CNC machines and robotic arms is improved; products are better produced with less waste in the production processes.
Operational Benefits of Machine Calibration and Optimization
Integrating artificial intelligence into the processes of machine calibration and optimization offers several advantages, including:
-
Improved Accuracy and Quality Management: With the help of agentic workflows, which can evaluate data instantaneously while the machine is running and adjust accordingly, it is possible to reduce or eliminate any possible quality variations during the production process.
-
Greater Efficiency: Combined with AI, optimization techniques also help discover the areas of wastage in the production system. Eliminating those faults assists the manufacturers in cutting back idle time, improving the turnover index, and hence earning more profits.
-
Lower Costs: Calibration and optimization processes can be substantially eased, making it possible to cut down on labor and eliminate wastage.
-
Performing Functions at Reduced Time Scale: Artificial intelligence also allows monitoring and management of operations at manufacturers’ plants within a very short period which can easily be termed as real-time.
-
Practical Applications and Evaluation of Performance: In addition, manufacturers stand to benefit from Agentic workflows by being able to explore the potential of data and gain useful information.
Technologies Transforming Machine Calibration
-
Internet of Things (IoT): The use of IoT Sensors allows for real-time monitoring of machine processes by tracking various parameters such as temperature, and vibration among others to maintain efficiency.
-
Machine Learning (ML): With enormous quantities of data accessible, ML technologies scan through the data and predict the likelihood of occurrence of outlier events which leads to wise decision-making ahead of time so as to reduce standbys.
-
Big Data Analytics: The analysis of large amounts of accurate information within a short time enhances the understanding of how a certain process carries out its operations thus aiding effective calibration management and making educated choices among firms.
-
Digital Twin: It without the accompanying risk associated with actual process alteration allows optimization of settings before making the changes using calibration techniques on actual machines.
-
Edge Computing: Edge computing allows lowering the latency of systems hence dynamic environments with real-time calibration that are directed toward faster adjustments can be adopted.
Future Trends in Machine Calibrations
In the future, the importance of artificial intelligence in manufacturing will be even greater. For instance, the IoT can connect to machines and gather a huge amount of information which includes the status of the machines and AI agents can use that information to adjust calibration and optimization changes in real-time.
-
Predictive Maintenance: Machine learning predictive has proven that not only does data received from machines help know when the breakdown is likely to occur, but repairs can also be localized before that happens. This maintenance strategy does not advocate waiting for the machine to fail saving on maintenance costs and maximizing the working life of the machine.
-
Supply Chain Effectiveness: AI takes care of logistics and repo inventory and also does demand prediction with the aim of improving the supply chain.
-
Training through Augmented Reality: This means that with the help of Artificial Intelligence along with Augmented when a workman is being taught or doing maintenance training instruction can be given in three dimensions.
-
Quality Control IoT: These intelligent systems possess artificial intellect and perform quality inspecting control of the production immediately using advanced imaging technology.
-
Statistics Modification: Complex AI analytics gives manufacturers the possibility to learn more about their operations and improves their ability to make decisions.
Conclusion: Agentic workflows in Machine Calibration
Machine calibration and optimization through AI agents are revolutionizing production and manufacturing by providing higher levels of accuracy, efficiency, and cost-effectiveness. When Agentic workflows are leveraged, there are boundless opportunities for manufacturers seeking to keep their business operations healthy in the changing landscape. Despite the slow uptake of these technologies, there are optimistic outlooks for the near future of Industries as manufacturing will largely be influenced by innovations driven by AI agents.
Agentic workflows help enhance the quality of machine calibration, which in turn minimizes flaws and enhances the quality of the end product. AI agent-powered optimization processes serve to enhance effective utilization of resources which propels the profitability of the business. There will be an emphasis on smart factories, green manufacturing, and human-robot interactions in the Manufacturing sector going forward.