Key Insights
Real-time asset health monitoring with AI agents boosts preventive maintenance, reducing downtime and increasing productivity. By analyzing data, manufacturers can detect early signs of failure and respond quickly to performance fluctuations. This shift enhances machine operations and paves the way for self-maintaining systems as AI evolves. Tools like GE Digital's APM concept show potential productivity gains of 30% and efficiency improvements of 25%, highlighting AI's transformative impact on manufacturing.
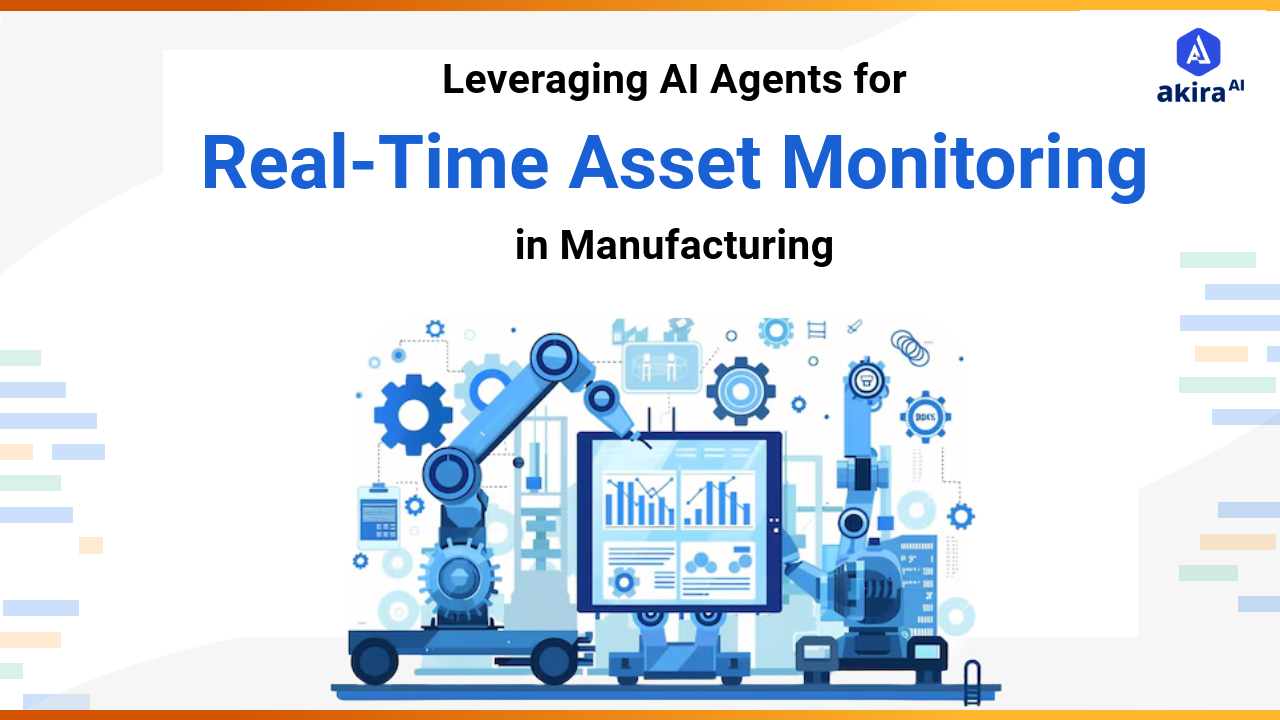
The manufacturing industry is evolving rapidly, and real-time asset health monitoring is at the forefront of this transformation. Powered by AI agents, this approach enables manufacturers to continuously assess equipment performance, predict potential failures, and minimize costly downtime.
Unlike traditional maintenance strategies, AI-driven monitoring leverages real-time data and machine learning to provide actionable insights, ensuring optimal asset utilization and improved operational efficiency. Companies adopting this technology aren’t just solving current challenges—they’re setting the foundation for smarter, more resilient manufacturing systems.
This article dives into the potential of AI agents in asset health monitoring and the hurdles manufacturers must overcome to fully embrace this innovation.
What is Real-Time Asset Health Monitoring?
Real-time asset health monitoring will entail a constant check on how the equipment is performing through IoT devices and AI algorithms-and in this regard, it pulls data from sensors fitted on the relevant machinery, with metrics that can be checked including temperature and vibration levels and how efficient the equipment is at what it is expected to do. Also, it enables one to detect potentials of failure before they cause production downtime and equipment breakdown which would facilitate optimum maintenance. Real-time monitoring also offers efficient decision-making by the use of data derived from the information that optimizes the schedule for maintenance together with the operation practice. This way, therefore, improves the management of asset integrity, whereby manufacturing processes flow more easily and effectively and are manufactured at the utmost lifespan and productivity of any equipment.
A Brief Overview of Asset Health Monitoring in Manufacturing
In the manufacturing domain, the utilization of asset monitoring was previously limited and primarily appreciated based on planned inspections and reactive maintenance. This created a problem because it expected surprise failures and expensive stoppages. This became inefficient because maintenance activities were performed regardless of the actual status of the equipment.
The current technology, particularly asset integrity management software, is pushing manufacturers toward adopting Asset Performance Management (APM). This approach works in tandem with or is supplemented by, predictive analytics and real-time data collection, allowing for continuous monitoring using IoT sensors to detect patterns and anomalies in equipment performance. However, the fact is that the maintenance strategies developed by the manufacturer can avoid product failures. This new approach enhances effectiveness and serves the need for reliability and performance in today’s highly regarded commercial market of optimal resource utilization and organizational operations.
Traditional vs Agentic AI Asset Health Monitoring
Feature |
Traditional Monitoring |
Agentic AI Monitoring |
Maintenance Approach |
Reactive maintenance (fixing issues after they occur) |
Proactive maintenance (predicting and preventing failures) |
Data Collection |
Manual data collection |
Automated, real-time data collection via IoT sensors |
Downtime Risk |
Higher risk of unexpected failures and downtime |
Reduced downtime, increased asset uptime |
Insights |
Limited insights based on inspections |
Advanced, predictive analytics for failure forecasting |
Automation |
Minimal automation |
High automation with self-monitoring and decision-making agents |
Efficiency |
Less efficient, leading to unnecessary maintenance |
More efficient with optimized resource utilization |
Akira AI Multi-Agent in Action
Fig1: Architecture Diagram of Real-time Asset Management
Asset health monitoring incorporates AI and multi agents in improving over efficiency and effectiveness in the management and execution of data processes. There will be a number of specialists and various applications that are approach oriented to making the simplification of the monitoring-related work possible.
-
Data Collection Agent: The Data Collection agent is continually gathering live data from sensors of IoT connected equipment which provides a continuous stream of information related to the performance status of the equipment which if detected may lead to early signs of anomalies.
-
Data Analysis Agent: The agent will gather, use an ML algorithm to recognize suitable patterns and anomalous behaviors, and through the data recorded in the past and the data collected in real-time, this agent will forecast failures and will ensure preventive measures are taken to avoid equipment breakdown.
-
Recommendation Engine: The Recommendation Engine will produce recommendation statements after a recommendable analysis of the maintenance decisions and enhance the efficiency of the maintenance decisions operation by making the decisions what should be done-that is, scheduling or replacing parts-and provide the decision with a data that was extracted from the maintenance operation.
-
Maintenance Agent: Maintenance Agent carries out or triggers people for prompt actions of recommended maintenance works. This cuts on aspects of possible equipment failure through automating repetitive tasks or timely actions concerning total asset availability and performance in terms of downtime. Such agents act in synchrony to constitute an essential system that supports improvement in real-time observation and preventive maintenance in production.
Use Cases of AI Agents in Asset Health Monitoring
-
Predictive Maintenance: By analyzing historical and real-time data, agents forecast when equipment will fail, allowing maintenance to be scheduled proactively. This approach minimizes unplanned downtime, extends asset life, and reduces repair costs.
-
Condition Monitoring: Continuously tracks asset performance indicators like temperature and vibration, identifying early signs of failure. Early detection allows for corrective actions before issues become serious, reducing the likelihood of unplanned downtime and optimizing asset performance.
-
Performance Optimization: Agents analyze operational data to identify inefficiencies, such as excessive resource consumption or production delays. By recommending improvements, such as process adjustments, the system enhances productivity, reduces waste, and lowers operational costs.
-
Lifecycle Management: Tracks assets’ conditions throughout their lifecycle to determine when maintenance, upgrades, or replacement is necessary. This ensures that assets are used efficiently, with timely interventions maximizing their operational value and minimizing unnecessary costs.
Operational Benefits of Asset Health Monitoring
-
Increased Automation: By 2025, automated monitoring will handle up to 80% of tasks, allowing human operators to focus on data analysis and higher-level decision-making, improving overall operational efficiency.
-
Enhanced Productivity: Automated maintenance and data analysis will improve productivity by 30%, ensuring assets perform at optimal levels, reducing downtime, and increasing throughput, which boosts overall manufacturing output.
-
Improved Efficiency: Automation and integrated workflows will improve efficiency by 25%, enabling timely maintenance, better resource allocation, and optimized operations that lead to significant improvements in production outcomes and work achievements.
-
Proactive Maintenance: By predicting equipment failures in advance, timely preventive actions will minimize unplanned downtime, maintain consistent production, and reduce the costs associated with reactive repairs and emergency fixes.
-
Cost Savings: Automating monitoring and maintenance, optimizing resource use, and reducing downtime will help cut operational costs, extend asset life, and ultimately improve the profitability and sustainability of manufacturing operations.
Technologies Transforming Asset Health Monitoring with AI Agents
-
IoT Sensors: These collect real-time information from the machinery and monitor critical parameters like temperature and vibrations. Such continued data feed proves extremely valuable in terms of asset performance because anomalies can be quickly discovered, and planned maintenance of assets can be done to prevent failures.
-
Machine Learning Algorithms: The algorithms through sensing devices of IoT empower predictive analytics. They can detect patterns and places where something may go wrong even letting manufacturers take proactive maintenance before problems appear thus saving on downtime and reduction of maintenance costs.
-
Cloud Computing: Its scalable storage and processing capability offer huge amounts of data generated. Easy access to this data along with sophisticated analytical tools designed for manufacturers, generating actionable insights beyond the boundary of local infrastructure.
-
The digital twins: Digital replicas of physical assets that simulate in real-time how a physical asset is performing. These can monitor and track conditions with testing scenarios to get insight into further informing decisions and optimization strategies.
The FutureTrends in Asset Health Monitoring
-
Augmented Reality: Future integration can include AR, through which the technicians can see visual overviews of the condition of an asset and thereby improve the efficiency of further troubleshooting, while on-site workers can make quick, well-informed decisions.
-
Enhances Interoperability: As the systems mature, AI agents are likely to hand over to different platforms. Data will be shared and collaborated in order to make up one integrated whole, streamlined asset management practice.
-
Fully Autonomous Maintenance: In this regard, high AI would enable systems to carry out maintenance totally autonomously. Problems would be addressed immediately, and staff would be able to do more sophisticated things.
-
Continuous learning: AI agents will improve their predictive ability through continuous learning from new data. In this way, it will enhance decision-making and help manufacturers adjust their maintenance strategies according to changed conditions.
Conclusion: AI Agents for Asset Health Monitoring
Real-time asset health monitoring driven by AI agents marks a significant advancement in the manufacturing sector. Here, manufacturers can improve their asset management practices using GE Digital's APM strategy together with IoT devices. This is an active step and increases operational reliability and efficiency while showing results in a more resilient manufacturing environment. Industry will transform, and embracing AI-solutions is one of the few available pathways leading toward sustaining competitiveness in this emerging digital-first environment.