Key Insights
Manufacturers need material flow optimization for efficiency and cost-effectiveness, coupled with sustainability. The lean manufacturing approach helps organizations remove bottlenecks and improve productivity. Material flow analysis identifies inefficiencies that should be targeted for improvement. AI agents working on aspects of inventory management and logistics optimization automate task. Integration of these intelligent systems will lead to operational excellence and competitiveness in an ever-changing market.
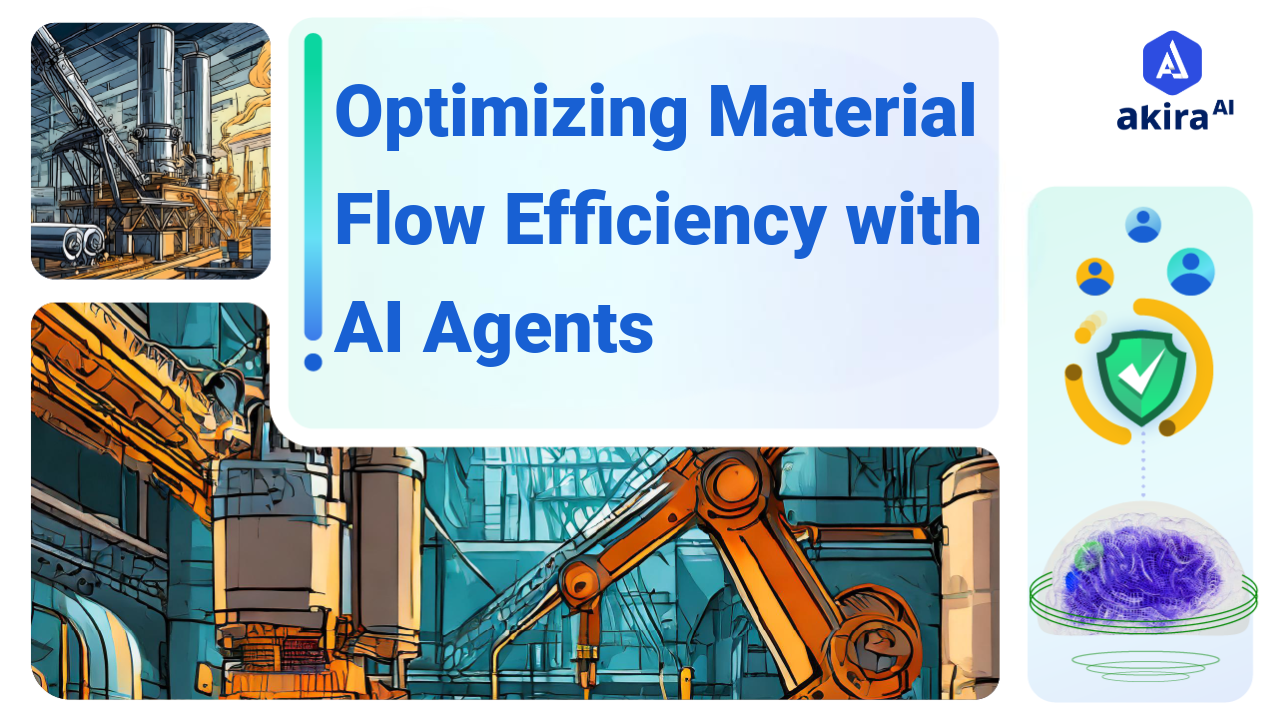
The manufacturing landscape is undergoing a significant transformation, with a growing emphasis on optimizing material flow to enhance efficiency and sustainability. As advancements in artificial intelligence (AI) and agentic workflows emerge, companies are discovering how these innovations can streamline operations, reduce waste, and improve productivity—hallmarks of lean manufacturing.
With sustainability trending in global conversations, manufacturers are poised to harness these technological advancements. Explore how AI Agents are reshaping operations, driving innovation, and paving the way for a more efficient, eco-friendly future in manufacturing.
What is Material Flow in Manufacturing?
Material flow in manufacturing describes the movement of raw materials and components through the production cycle until a finished product is delivered to the consumer. Such a process is very important to any manufacturing firm since it directly affects the efficiency and effectiveness of the production of products. Proper material flow management will ensure that there is the efficient usage of all resources and timeliness of schedules for the manufacture. There will be automatically achieved waste reduction.
Besides being important for general financial health, it will prove useful in facilitating an on-time product delivery to the customers. A very streamlined flow will, of course, be sure to enhance the management of more inventory, lesser lead times and increased customer satisfaction being necessary requisites for the maintenance of a competitive advantage in markets.
A Brief Overview of Material Flow Optimization
Material flow optimization has evolved significantly over the years, driven by technological advances and changing manufacturing demands. The journey from manual tracking to modern AI-powered systems represents a fundamental shift in how manufacturers approach material management:
-
Historical Context: Traditional material flow relied heavily on manual processes and static routing, leading to inefficiencies and bottlenecks.
-
Current State: Modern material flow optimization incorporates real-time data analytics, IoT sensors, and automated systems to create more dynamic and responsive workflows.
-
Future Direction: The integration of AI agents and agentic workflows represents the next evolution in material flow optimization, promising unprecedented levels of automation and efficiency.
Traditional vs. Agentic AI in Material Flow Optimization
Agentic AI refers to systems that operate with a degree of autonomy and decision-making capability. In the context of material flow, agentic AI can facilitate complex workflows, coordinating multiple processes and agents to optimize production efficiency.
Aspect |
Traditional Approach |
AI Agent-Based Approach |
Decision Making |
Manual analysis and predetermined rules |
Real-time, adaptive decisions based on multiple data points |
Response Time |
Hours to days |
Immediate to minutes |
Optimization Scope |
Limited to specific areas |
End-to-end optimization across the entire supply chain |
Predictive Capabilities |
Basic forecasting based on historical data |
Advanced predictive analytics with multiple variables |
Resource Allocation |
Static allocation based on fixed schedules |
Dynamic allocation based on real-time demands |
Waste Reduction |
Reactive approach to identifying waste |
Proactive waste prevention through predictive analysis |
Workflow Adaptation |
Manual process changes |
Autonomous workflow adjustments |
Cost Optimization |
Periodic cost analysis and adjustments |
Continuous cost optimization in real-time
|
Akira AI Multi-Agent in Action
Fig1 : Key Components of the Material Flow with AI Agents
In a multi-agent framework, various AI agents collaborate to optimize material flow, each with specific roles:
-
Orchestrator Agent (CA): The Orchestrator Agent acts as the central coordinator, aligning all other agents with overall production goals. It continuously gathers real-time data on production requirements, resource availability, and facility conditions.
By analyzing this data, the CA identifies needs, detects potential bottlenecks, and assigns tasks to the operational agents. Through ongoing communication, it ensures a smooth workflow across the system. The CA also adapts processes and priorities as conditions change, keeping production efficient and responsive.
-
Planning Agent (PA): The Planning Agent is responsible for creating detailed production schedules based on current demand forecasts, resource availability, and inventory levels. It receives input from the Orchestrator Agent to ensure alignment with overall goals.
Once the schedule is complete, the PA shares it with the Routing Agent and Inventory Agent for coordinated execution. The PA continuously updates plans as demand or resources shift, ensuring that production remains efficient and resources are well-utilized.
-
Routing Agent (RA): The Routing Agent optimizes material transport routes within the facility, supporting efficient material flow. It receives production schedules from the PA, analyzes facility layout, and determines the best routes for moving materials. The RA communicates these routes to the Execution Agent (EA) for implementation, continuously monitoring and adjusting paths as needed to avoid delays. By ensuring smooth movement of materials, the RA helps maintain an uninterrupted production process.
-
Inventory Agent (IA): The Inventory Agent manages stock levels and ensures that materials are available for production when needed. It monitors inventory data in real-time, alerting the Orchestrator Agent (CA) if stock levels are low or there’s an overstock issue. This proactive approach prevents disruptions, as the IA also provides relevant inventory data to the Planning Agent for accurate scheduling. By keeping optimal stock levels, the IA minimizes risks of material shortages and maintains production flow.
-
Quality Agent (QA): The Quality Agent ensures that all products meet established quality standards. By performing real-time monitoring and inspections, the QA identifies and addresses quality issues as they arise.
It receives production data from the Planning Agent and execution details from the Execution Agent (EA), using this information to conduct thorough checks. The QA communicates any quality concerns to both the CA and EA, enabling immediate corrective action and maintaining high production standards.
-
Execution Agent (EA): The Execution Agent integrates inputs from other agents to perform tasks on the production floor. It receives schedules from the Planning Agent (PA) and routing information from the Routing Agent (RA), converting these into actionable instructions for the physical systems.
By coordinating task timing and monitoring progress, the EA ensures smooth execution of workflows. The EA also receives performance feedback from the Monitoring Agent (MA) and makes adjustments as needed to keep operations aligned with the CA’s directives.
Applications of AI Agents in Material Flow
-
Supply Chain Optimization:
AI agents enhance procurement and inventory management by analyzing demand patterns and supplier performance. This ensures that necessary materials are available precisely when needed, reducing delays and excess stock. As a result, manufacturers can maintain a leaner and more efficient supply chain.
-
Production Scheduling:
Real-time data from the production floor allows AI agents to adjust schedules dynamically based on current conditions. This flexibility enables manufacturers to respond quickly to changes in demand or unexpected disruptions. Consequently, it improves overall operational efficiency and resource allocation.
-
Waste Reduction:
AI agents identify inefficiencies in material usage and suggest actionable improvements to minimize waste. By analyzing production processes, they can recommend optimizations that lead to better resource utilization. This not only enhances sustainability but also reduces costs associated with excess material.
-
Quality Control:
Continuous monitoring of production quality enables AI agents to detect deviations from standards in real-time. By implementing prompt corrective actions, these systems help maintain high-quality output throughout the manufacturing process. This proactive approach significantly reduces the risk of defects and enhances customer satisfaction.
-
Predictive Maintenance:
AI agents leverage historical data and real-time monitoring to anticipate potential equipment failures. By addressing maintenance needs before issues arise, manufacturers can minimize downtime and ensure a smooth, uninterrupted flow of materials. This proactive strategy leads to enhanced productivity and cost savings.
Operational Benefits for Material Flow Optimization
-
Enhanced Productivity:
By 2025, AI agents are expected to automate at least 80% of operational tasks, drastically improving workflow efficiency. This high level of automation not only speeds up processes but also allows human workers to focus on more complex and creative tasks. The result is a significant boost in overall productivity across manufacturing operations.
-
Efficiency Gains:
AI-driven enhancements can lead to operational efficiency improvements of up to 25%, all without increasing resource consumption. By streamlining processes and minimizing waste, manufacturers can optimize their workflows and achieve more with the same resources. This efficiency is key to sustaining competitiveness in a rapidly evolving market.
-
Cost Reduction:
Implementing AI leads to substantial cost savings through reduced waste and optimized material handling. Efficient management of material flows ensures that resources are used wisely, contributing to lower operational costs. As a result, manufacturers can enhance their bottom line while promoting sustainability.
-
Enhanced Decision-Making:
AI systems provide real-time information that empowers machines and operators to make better strategic decisions. By facilitating proactive adjustments based on current data, these systems improve outcomes across the board. Enhanced decision-making capabilities allow manufacturers to respond swiftly to changing conditions, ultimately leading to greater success.
-
Increased Output:
AI can potentially increase manufacturing output by approximately 30% through optimized workflows and minimized downtime. Quick decision-making and efficient processes enable manufacturers to produce more in less time, significantly boosting productivity and profitability. This increase in output positions companies favorably in competitive markets.
-
Reduced Labor Costs:
The automation of repetitive tasks by AI leads to a decrease in reliance on human labor, which helps reduce overall labor costs. With fewer employees needed for routine tasks, manufacturers can redeploy human resources to more complex work that requires critical thinking and creativity. This shift not only enhances productivity but also improves the return on investment as more is produced with less labor.
Technologies Transforming Material Flow with AI Agents
-
Machine Learning: Enhances demand forecasting and inventory management by analyzing historical data for better accuracy, reducing excess stock and costs.
-
Internet of Things (IoT): Provides real-time data from sensors to improve visibility and responsiveness in material flow, enabling immediate operational adjustments.
-
Robotic Process Automation (RPA): Automates repetitive tasks to free up human resources for complex activities, increasing productivity and employee satisfaction.
-
Cloud Computing: Offers scalable data storage and processing, allowing manufacturers to access and analyze information flexibly, enhancing agility in operations.
-
Blockchain: Ensures traceability and transparency in material flows by creating an immutable ledger of transactions, fostering trust and compliance across the supply chain.
Future Trends in Material Flow Optimization
-
Greater Integration: Future AI tools will seamlessly connect with existing manufacturing systems, enhancing their functionality and promoting smoother operations. This will allow for better utilization of data and processes, minimizing disruption during implementation.
-
Advanced Analytics: Sophisticated analytics will provide deep insights into material flows and operational efficiency. By analyzing historical and real-time data, manufacturers can pinpoint bottlenecks, predict trends, and make informed decisions that optimize production and reduce waste.
-
Decentralized Decision-Making: Empowering teams at various levels to make informed decisions quickly will enhance agility in responding to fluctuations in material availability and demand. This approach allows frontline workers to adapt swiftly to unforeseen challenges in the supply chain.
-
Sustainability Focus: Future applications will prioritize waste reduction and environmentally friendly practices in material handling. By identifying inefficiencies and recommending sustainable alternatives, manufacturers can meet regulatory requirements and corporate social responsibility goals while maintaining productivity.
Conclusion: AI Agent for Material Flow Optimization
This interconnection of AI agents with agentic workflows in material flows is a transformative opportunity in manufacturing. Organizations embracing this technology can optimize their workflow, reduce waste, and increase productivity according to lean manufacturing principles. The transformation of the industry will unlock more potential for AI and reshape material flow in further efficiency and sustainable manufacturing processes.
By focusing on the intersection of technology and manufacturing processes for companies, they will ensure they stay ahead in the future complex market landscape. Moving forward, material flow optimization is not just about effectiveness but about using intelligent systems to create a more responsive, agile, and sustainable manufacturing environment.