Key Insights
Agentic AI is transforming manufacturing by optimizing yield and batch analysis in real-time. These systems continuously monitor production, make data-driven adjustments, and predict maintenance needs, ensuring maximum efficiency, reduced waste, and higher product quality. By automating routine tasks, AI agents allow human operators to focus on complex decisions, driving productivity, scalability, and cost savings. The future of manufacturing lies in the seamless integration of AI, enhancing operational performance and enabling smarter, faster production cycles.
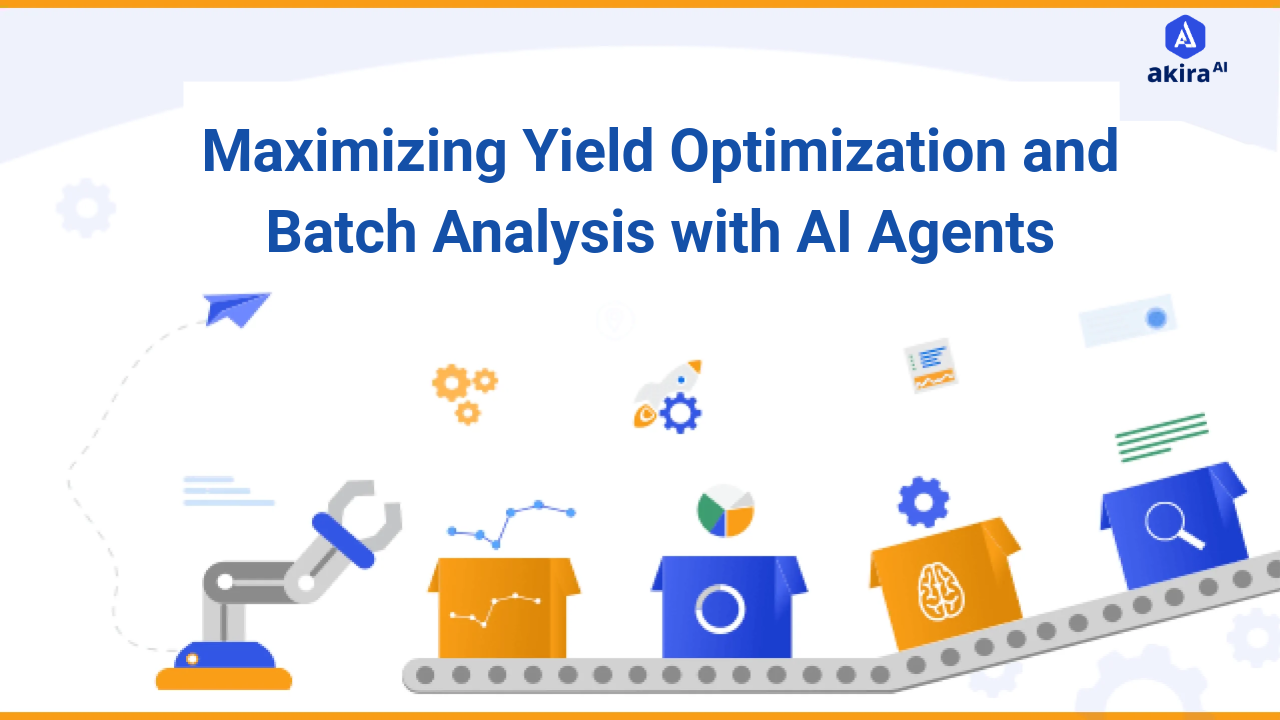
In the evolving landscape of modern manufacturing, the strategic maximization of yield optimization and batch analysis plays a crucial role in enhancing productivity, efficiency, and product quality. These techniques aim to increase output, reduce waste, and lower operational costs. With the advent of agentic AI, these methods have become more sophisticated and precise. AI agents, working alongside human operators, analyze complex data patterns, make real-time adjustments, and suggest improvements to ensure that production lines run at their maximum capacity. This collaboration between agentic AI and human expertise is driving a new era of smart manufacturing, where operational efficiency and quality are optimized through advanced, data-driven insights.
What is Yield Optimization and Batch Analysis?
Maximize yield optimization and batch analysis for more efficiency. Maximizing yield optimization and batch analysis are strategies for productivity enhancement to avoid wastage, defects, and resource consumption. Optimizing yield ensures that all processes yield maximum product quality, while batch analysis keeps on checking production batches to pinpoint inefficiency or lack of proficiency to tweak the operation in real time. This maximizes manufacturers' ability to increase productivity, save costs, and ensure the stable quality of their products. With the aid of Agentic AI technology, they provide a basis for smarter data-informed decisions for manufacturing process efficiency.
Overview of Maximizing Yield Optimization and Batch Analysis in Manufacturing
The AI teammates are transforming the face of manufacturing by standing guard over every step of production in vigilant monitoring. These conventional systems were monitored merely through manual oversight or a few random checks. But in AI, this vigilante monitoring occurs in real-time, and sophisticated machine learning models find inefficiencies or deviations from production patterns. At that very moment, the AI recommends corrections. Real-time adaptability in manufacturing supports quick reactions to issues and minimizes downtime and waste generation.
In batch analysis, AI teammates improve quality control by checking each production batch for consistency and quality using historical data and real-time insights. Using such an approach, manufacturers can predict eventual disruptions by identifying early indicators of probable failures or inefficiencies in the process. The early detection allows the manufacturing process to keep running efficiently without expensive mistakes and high standards on all runs.
Traditional vs. Agentic AI Yield Optimization And Batch Analysis
Aspect |
Traditional Approach |
Agentic AI Yield Optimization |
Data Processing |
Manual entry, processing, and analysis |
The system that would collect, process, and provide automatic real-time data input |
Accuracy |
Human error-prone, restricted due to manual computation |
Guarantees high precision levels as the cases detected are checked upon through machine learning models |
Speed of Optimization |
It has a slow response time because manual analysis is done |
Real-time optimization eased through algorithms |
Scalability |
Impossible to be extended into many productions' lines |
Scalable easily in different production settings |
Predictive Insights |
With very limited predictive capability |
Algorithm and data analytics enabled by AI Agents predict and optimize beforehand |
Workload on Human Operators |
It has a high workload because it is to monitor and modify constantly |
The workload is significantly reduced with AI handling the repetitive tasks |
Decision-Making |
It requires the capability of the operator to experience |
Data-driven decisions provided by AI Agents to make recommendations |
Use Cases and Applications of Maximizing Yield Optimization and Batch Analysis
-
Predictive Maintenance in Electronics Manufacturing
AI agents improve yield in electronics manufacturing by performing predictive maintenance on high-precision equipment like PCB assembly and soldering machines. By analyzing data such as temperature, vibration, and speed, they anticipate potential malfunctions, enabling preemptive adjustments to avoid breakdowns. This reduces downtime, enhances yield quality, and minimizes defects.
-
Process Optimization in Solar Cell Manufacturing
In solar cell production, AI agents monitor variables like light exposure, material thickness, and chemical deposition. Through real-time adjustments, they improve efficiency and durability, ensuring consistent quality while reducing material waste. AI agents also utilize predictive models to maintain optimal production conditions, increasing yield.
-
Anomaly Detection in Semiconductor Lithography
In semiconductor lithography, AI agents manage sensitive variables like laser focus and exposure. By monitoring data and adjusting it in real-time, they reduce the risk of defects, ensuring a high yield of functional chips and maintaining chip performance and reliability.
-
Resource Allocation in Battery Manufacturing
AI agents in battery production monitor variables like electrode coating and drying temperatures to maximize yield and reduce cycle time. By dynamically adjusting parameters, they enhance energy density and prolong battery life, supporting high-performance demands while minimizing waste in electric vehicles and consumer electronics production.
Akira AI Multi-Agent in Action
Fig1: Agentic Workflow of Yield Optimization and Batch Analysis
Akira AI's multiagent system will enable collaboration in the AI agents to automatically perform a core manufacturing role while providing continuous improvements in yield optimization and batch analysis without human interventions. They analyze data at various stages of development, and these Akira AI agents provide predictions and real-time adjustments while ensuring quality, all for maximum yield with little or no defects. This enables Akira to produce a smart and autonomous manufacturing environment where operational efficiency is constantly optimized.
-
Automatic Core Manufacturing Operations with Akira AI Agents
Akira AI’s multiagent system powers automated core manufacturing processes, with each agent collaborating to streamline critical production tasks. These agents operate through an intelligent distributed network, autonomously coordinating roles and reducing dependency on human supervision.
-
Continuous Yield Optimization and Batch Analysis by AI Agents
Akira AI agents monitor yield and quality metrics at every stage of production, identifying areas for improvement in real-time. By suggesting adjustments on the fly, agents help achieve maximum output with minimal defects, enhancing uniformity across each batch.
-
Data-Driven Decisions and Real-Time Adjustments by AI Agents
Throughout the production line, AI agents collect and analyze data, allowing for informed, data-driven decisions. Leveraging historical patterns and current conditions, agents make real-time adjustments to address inefficiencies, enhancing quality without disrupting the workflow.
-
Predictive Maintenance and Failure Prevention with AI Agents
Akira AI agents continuously monitor equipment and system health to detect early warning signs of disruptions. With predictive capabilities, they identify potential failures before they impact production, enabling preemptive interventions.
Operational Benefits of Yield Optimization and Batch Analysis
-
More Productivity: AI agents do more complex tasks of repeating work and vast data analyses than the human mind. They will be able to manage 80% of the operational processes by 2025, freeing human operators for more complex jobs. This automation shows a 30% productivity improvement in production lines.
-
Better Efficiency: This results in improved operational efficiency by a factor of 25% as AI teammates monitor round-the-clock production and conduct real-time optimization of parameters. This leads to reduced downtime, energy consumption, and maintenance of consistent quality of products.
-
Reduced Operational Expenses: The use of agentic workflow for yield optimization leads to reduced wastage of materials, energy consumption, and defective products. This results in an overall significant reduction in the cost of production.
-
Improved Quality Control: Thanks to real-time analysis of batch data by AI teammates, the chances of defective products are less frequent, and therefore, the desired quality yields are fulfilled with the delights of their customers.
-
Faster Time-to-Market: AI agents further enable manufacturers to speed up their production cycles, right from raw material handling to assembling the final product. That speeds up the time that is required to launch new products onto the market.
Technologies Transforming in Yield Optimization and Batch Analysis
-
Predictive Analytics and Machine Learning Models: AI agents use predictive models to anticipate potential issues in production. Machine learning algorithms analyze historical and real-time data, helping agents make proactive adjustments to maximize yield and maintain consistency across batches.
-
Automated Guided Vehicles (AGVs) and Robotics: AGVs and robotic systems collaborate with AI agents to transport materials and manage repetitive tasks. By automating logistics, they ensure seamless material flow, reducing bottlenecks and enhancing throughput for optimized yield.
-
Advanced-Data Analytics and Cloud Computing: Cloud-based analytics platforms enable agents to access and analyze large datasets. By leveraging centralized data processing, AI agents can identify trends, make data-backed adjustments, and continuously refine production methods for maximum yield.
-
Autonomous AI Agents and Multiagent Systems: Autonomous AI agents function as specialized units responsible for various tasks, like defect detection, resource allocation, and maintenance. Multiagent systems enable these agents to collaborate, dynamically adjusting production parameters and ensuring continuous yield optimization.
The Future Trends for Yield Optimization and Batch Analysis
-
Increased Autonomy: AI agents should handle the whole production line on their own, requiring minimal human intervention for increased overall manufacturing efficiency.
-
Self-Optimizing Systems: In future AI, it will not just offer recommendations but automatically, real-time change parameters to continue maximizing yield without any input from the operators.
-
Real-time adaptation to market changes: AI agents will be able to analyze demand trends and, based on those analyses, adjust production rates so that it is not overproduced, and hence output will be matched by the demand in the market.
-
Agentic AI-driven personalization: Manufacturers will be able to mass-produce hyper-personalized products with the power of AI agents, responsive to needs, maximizing yield and efficiencies.
Conclusion: AI Agents for Maximizing Yield Optimization and Batch Analysis
AI teammates change the manufacturing optimization approach in making yield, and they enhance the analysis of batch production by completely automating data collection, analysis, and decision-making. Their extreme improvements in productivity, efficiency, and quality of products make it possible to predict disruptions, adjust parameters in real-time, and monitor production continuously with AI agents. It will give manufacturers the ability to attain higher yield levels while keeping costs minimal. The future of manufacturing is poised to be more autonomous, with AI agents at the center for steering and additional augmentations of operational excellence as AI evolves.